Stages of manufacturing a complete removable denture. Evaluation of prosthetic results. Removable prosthetics: acrylic plastic
Author of the article:
Anastasia Vorontsova
In the application of complete removable dentures Most often, people in the older age group need it, who, as a rule, already have some experience in using dental structures.
The number of patients suffering from complete edentia is gradually increasing, so the issue of high-quality prosthetics is relevant at the present time.
The manufacture of removable dentures involves certain laboratory and clinical stages.
Close interaction between the dentist and the dental technician during the manufacturing process ensures the success of dental prosthetics.
The specifics of the work depend not only on the clinical situation in the oral cavity, but also on the patient’s mood.
- Before starting prosthetics, it is necessary to find out from the patient whether he has experience in using dental structures. If: “yes,” then did the patient experience any discomfort when using the prosthesis.
- In order to identify the condition of the jaw bone tissue, soft tissue anomalies and other abnormalities, a clinical and radiological examination of the patient’s oral cavity is mandatory.
- In some cases, before prosthetics, surgical interventions to remove impacted teeth or alvelectomy may be performed. This approach allows the doctor to make high-quality dentures.
- Carrying out psychological preparation the patient before starting prosthetics plays an important role in achieving success.
Manufacturing stages
Technology The manufacture of removable structures includes two stages: clinical and laboratory.
Before the production of the prosthesis begins, planning and assessment of the aesthetic parameters of the patient who will use the dental structure is carried out:
- Evaluated appearance the patient and his facial features.
- The shape and shade of artificial teeth are selected taking into account the appearance of the dentition when smiling and talking.
Stages of manufacturing a complete removable denture can be represented this way:
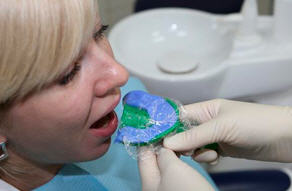
- Examination of the patient, diagnosis of the condition of the dental system, selection of a suitable design.
- Taking an impression from the jaw using a standard impression tray. Depending on which design is chosen, the impression mass is selected.
- The dental technician uses plaster models of the jaws to create custom impression trays.
- Taking impressions using individual trays.
- On working models, a wax base with occlusal ridges is made.
- Using rollers, the relative position of the jaws is determined.
- Strengthening the working models and occlusal ridges in the articulator.
- Making a future prosthesis from wax with acrylic teeth.
- Checking the structure in the oral cavity, assessing occlusion, fit, and aesthetics.
- Final modeling of the wax structure.
- Plastering the wax composition into a ditch and replacing the wax with acrylic.
- Polymerization of acrylic plastic, removal of the structure from the cuvette.
- Finishing of the prosthesis, grinding and polishing.
- The finished structures are fitted, the fit, occlusion and aesthetics of the prosthesis are checked.
- If necessary, the prosthesis is sent to the laboratory for modification.
- Delivery of the structure to the patient.
How to make
Technique manufacturing structures comes down to the following steps:
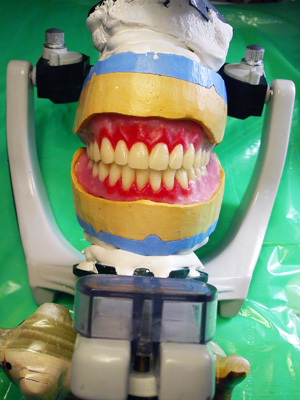
- To make plaster models, the dental technician fills the impressions of the jaws with plaster. Dentures are made using plaster models.
- The resulting models are installed relative to each other so that the distance between them, both horizontally and vertically, coincides with the true distance between the patient’s jaws.
- For this purpose, bite ridges are made from wax in laboratory conditions.
- To obtain a more accurate impression, an individual impression tray is made. It is made from acrylic and is a temporary plate that the dental technician models on a model.
- The finished wax rolls are given to the doctor to determine the occlusion.
- Models with rollers are sent to the laboratory. After installing the models in the articulator, the rollers are removed, and instead of them, acrylic teeth are fixed using wax.
- Fitting is carried out - trying on the wax prosthesis with teeth. The doctor checks the occlusion and aesthetics of the structure. Due to the fact that the teeth are fixed with wax, the production of dentures at this stage allows you to change the position and shade of the teeth.
- After the structure is corrected, it is sent to the dentist’s office.
In the process of manufacturing a complete removable denture, the volumetric modeling method is used.
Volumetric modeling of a complete removable structure is a procedure whose goal is to form the surface of the prosthesis, which corresponds to the relief of the tissues surrounding the structure and the volume necessary to maximize the filling of the prosthetic space.
Ideally, the following conditions should be met:
- The structure must fill the entire prosthetic bed.
- The polished surface of the prosthesis should follow the relief of the surrounding tissues.
If these requirements are met, the denture will be firmly fixed in the oral cavity while performing its functions.
Video: “This is how artificial teeth are made”
Evaluation of prosthetic results
The results of the treatment are assessed in the following areas:
- Based on subjective criteria: the patient’s feelings at the time of construction and after two weeks and a month.
- According to objective criteria: implemented using chewing tests and other additional research methods.
Repair
Breaking prosthesis is a fairly common phenomenon that can be caused by the following reasons:
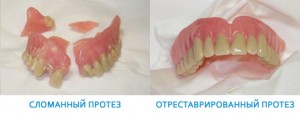
- Unsatisfactory quality of material.
- Severe clinical conditions in the oral cavity.
- The dental technician’s technology for manufacturing the structure was violated.
- Poor quality of clinical examinations by a dentist.
- Careless use of dentures by the patient.
- Presence of porosity in plastic teeth.
- Microcracks in porcelain teeth.
- Wear of plastic.
Type of failure:
- Loss or breakage of an artificial tooth.
- A complete breakdown of the structure.
- Presence of a crack in the prosthesis.
Regardless of the cause and type of structural failure, it is necessary to correct the situation. Urgent production of removable dentures? Maybe. But this will take some time. Not everyone can manage without teeth for a few days.
If the structure breaks down, you must contact the dental clinic, where a decision will be made about the possibility of repairing the prosthesis.
Video: “Removable dental prosthetics”
Moscow cosmetic factory "Svoboda" is one of the few ancient industries, still working almost in the center of Moscow (Dmitrovskaya metro station). Its history begins in 1843, with the first perfume factory in Russia, the Partnership “A. Ralle and Co. (since 1930, perfumes are no longer produced). Today, the factory's products include dozens of products: toothpaste, soap, shampoos, creams and gels, hair balms, shaving and aftershave products, children's cosmetics, serums, cleansing tonics and milk, etc. I think that Svoboda products are well known to you all. For example, I buy for my child only their “Children’s” cream in a metal tube (it has been produced since 1954 and today more than 400 million pieces have been produced), and I also love toothpaste"Periodontol".
Let's go with me to the factory and see how toothpaste is made.
Toothpaste production begins on the highest floors of the building. The final stage - packaging - occurs at the very bottom.
The first stage is the mechanical purification of tap water for further cooking of pasta. On the right in the photo you can see almost two-meter blue filters - there are 6 of them in total - 2000 liters. Then the water is ozonized for disinfection. And after that the ozone is destroyed using ultraviolet lamps so that it doesn't get into the paste. That's it, the water is completely ready for further use. Purified water is supplied to top floor where the cooking equipment is located.
The base for toothpaste (water + silicon dioxide (abrasive) + sorbitol (humectant, glycerin was previously used) + cellulose (thickener) + other) is boiled in such reactors. There are 5 of them at the factory. One reactor is capable of welding 3 tons of paste at a time, that is, for 25,000 tubes.
To prevent the paste from stratifying, it is cooked at a temperature of 40 degrees C. The mass is heated using the so-called steam jacket of the reactor - a thickening at the base of the reactor. There is a special mixer in the reactor, which constantly mixes the mass during cooking with at different speeds.
Reactor control panel.
The same reactor is used for cooking different types pastas (there are several dozen of them at Svoboda). To do this, after each use, the reactor and all pipes (they are dismountable) are washed. The cooked pasta is sent through pipes (so that it does not come into contact with air) into special containers for temporary storage. The photo shows just the tip of the iceberg. The main part of the vault is visible on the floor below.
After cooking, the pasta is taken from this hopper to laboratory research: compliance with the recipe (viscosity, density, color, smell), microbiological indicators, acid-base balance. The analysis lasts 3 days and only if everything is normal, the paste is sent to packaging.
Lots and lots of pasta.
We return again to the lower floor, where we saw water purification. Here you can see the second part of the paste storage containers.
The pipeline goes into the floor for packaging.
Everything is signed. Paradantol "Green tea", "Cedar", "Antibacterial"...
Packing. Tube filling machine.
Future tubes.
Pay attention to the dark mark on the ends of the tubes. Once Malysheva said in her program that high-quality natural toothpaste can supposedly be distinguished by this very mark - natural toothpaste is green. Lies. This label has nothing to do with the quality of the paste. It is used to orient the position of the tube in the tube filling machine (light marker). And it can be any color, depending on what ink you purchased.
These are all kinds of extracts (chamomile, green tea, calendula...). Also, during production, vitamins, colloidal silver (disinfects), sea minerals, food coloring, etc. can be added to the paste.
Exclusive pasta is ready.
And this is how they make tri-color toothpaste. The whole secret is in the clever design of the tube.
This concludes the story about the production of toothpaste. Original post in my journal
These dentures are made from various materials in specialized laboratories by dental technicians, in contrast to their usual restoration, which can be performed by a dentist in his clinic. Thanks to modern technologies for making dentures, they have become almost indistinguishable from real teeth.
Technique for making dentures
Making dentures is on the border between science and art, and the dental technician himself is like an artist or sculptor. He selects materials, gives the prosthesis the necessary color and shape, and creates the desired relief of the teeth, similar to the relief of the patient’s healthy teeth.
Preparation for prosthetics
Before making dentures, the patient must undergo a preparation procedure. It consists of maximum cleaning of teeth and gums from all defects and deposits. If there is caries on the teeth, it is cured, and the dental defect is filled. All tartar and other deposits are removed. The doctor may suggest that the patient undergo a teeth whitening procedure, which will make it possible to make a prosthesis with maximum compliance with the anatomical formations of the jaw. This concludes the preparation process.
Taking impressions
After preparatory stage Impressions are taken of the desired jaw in order to create a model for the jaw. Impressions are made with a special impression tray containing a plastic mass. This spoon is inserted into the patient's mouth to take an impression of the teeth.
Jaw mockup
The impressions taken are transferred to the dental technician in a specialized laboratory. In this laboratory, the casts are filled with plaster, which hardens and acquires all the necessary contours of the teeth and jaw needed by the dental technician. Dentures are made on the basis of this model.
Materials used to make dentures:
- plastic;
- acrylic;
- zirconium;
- pressed ceramics;
- nylon;
- silicone;
- metal ceramics;
- polyurethane;
- byugel and others.
Depending on the material used, dentures receive certain properties. Nylon and polyurethane give prosthetics flexibility, while acrylic and metal-ceramics give strength and aesthetic appearance.
Manufacturing of fixed dentures
Fixed dentures include:
- dental bridges;
- dental crowns;
- ceramic inlays;
- veneers.
Previously, dentures were made by stamping, but this method is outdated, since with its help it was not possible to achieve a good fit of the prosthesis to the anatomical formations of the jaw.
At the moment, the casting method is considered more effective. The injection molding technique for making dentures is more complex and expensive, but it allows for the production of truly high-quality dentures compared to stamped dentures. Clasp and metal-ceramic dentures are made using this method.
To make zirconium prostheses, special milling devices are used.
To process pressed ceramics, pressing furnaces are used, after which they are fired in special equipment.
Manufacturing of removable dentures
Thanks to the improvement of technologies for the manufacture of removable dentures, it is no longer necessary to constantly keep them in a glass of water in order to avoid the appearance of cracks on them due to drying out. Now they are made using casting and pressing of plastic. Therefore, current dentures do not require constant hydration, have a more aesthetic appearance and increased strength.
To make nylon dentures, special devices are required. These devices allow you to melt nylon granules. This molten substance is poured into special molds using the hot injection method.
Price for manufacturing various dentures
The cost of manufacturing dentures depends on a number of factors, among which the main place is occupied by the production technology itself, the material used, its quantity, and the reputation of the clinic.
Thus, a partial denture made of acrylic costs from 3,000 to 5,000 rubles.
Complete dentures made of acrylic - from 8,000 - 10,000 rubles.
Nylon prostheses cost from 13,000 – 15,000 rubles.
Clasp dentures – from 18,000 rubles.
The wide variation in the cost of dentures allows people in different financial situations to choose them.
Dental prosthetics is a very expensive, but necessary procedure for a full life. For the sake of saving budget, before buying a crown, it is advisable to monitor prices, and to help the reader, this publication presents detailed review orthopedic services in Moscow clinics with an indication of their cost.
The cost of prosthetics in different regions of Russia can vary greatly depending on the level of consumer ability of the population, as well as a number of factors that accompany the activities of any dental clinic: purchase cost of materials, rental of premises and public utilities, employee salaries, depreciation of expensive equipment, taxes, etc.
Prosthetics with removable structures has always been one of the most vital necessary services for different segments of the population. It costs much less than implantation, allows you to restore partially or completely lost teeth and, in addition, has many types designed for any clinical case and income.
Most quality option removable design - made of nylon.
– orthopedic design, which is a curved arch with teeth attached to it. Indications for its use are complete absence of teeth in the upper and/or lower jaw. The production of a complete removable denture takes place in two stages: during the first visit, the orthopedic dentist takes an impression of the gums, and during the second, a fitting is carried out. As a rule, this happens very quickly and takes from 3 to 10 days. On the upper jaw, the prosthesis is fixed due to the natural ability of the mucous membrane to suck in polymer materials (acrylic, plastic, nylon). The design has a number of disadvantages:
- wears out quickly
- over time, it begins to hold poorly, which makes chewing much more difficult, especially hard or sticky food,
- blocks the hard palate, causing nausea and discomfort,
- negatively affects articulation.
Most the best option is a product that is lightweight, has good aesthetic properties and has an opening in the area of the palatal support, which significantly reduces discomfort.
Despite the fact that the installation of removable dentures is considered a thing of the past and is recommended as a temporary solution for the period while a permanent structure is being made, it is used among older people in great demand. The reason is simple – the price is low compared to implantation.
A completely removable denture requires not only regular medical supervision, but also careful home care. Before going to bed, it must be removed, washed, cleaned with toothpastes and placed in a container with an antiseptic solution.
Partially removable structures have metal elements.
Partially removable denture It is placed in cases where there are at least a few healthy teeth or roots left in the patient’s mouth that can serve as support. The design is so named because it does not have to be stored overnight in a special liquid, but it must be removed (preferably daily) for thorough cleaning, since food debris can become clogged under it, irritating the gums and causing an unpleasant odor.
The indication for its installation is a significant absence of teeth (usually chewing ones). The manufacture of a removable partial denture almost always involves the presence metal parts– arches, attachments (locks) or clasps (fasteners). This nuance has a positive effect on the strength and longevity of service, allowing you to chew food of any hardness without problems, but at the same time it increases the cost of the product.
There are several main types of partially removable structures:
- – comfortable, strong and durable dentures based on metal arc. Thanks to this particular detail, the load in the clasps is distributed evenly, which reduces friction of the gums, prevents their atrophy and significantly shortens the period of adaptation.
- – a type of postoperative constructions applied to the gums immediately after tooth extraction. They promote rapid healing of soft and correct formation bone tissue, and also mask the absence of teeth during the period of prosthetics. Used as a temporary measure.
- Removable segments with one-sided fastening are made from inexpensive polymer materials and replace several missing teeth in cases where the use of clasp dentures is for some reason difficult or completely impossible.
- Butterfly dentures– small temporary structures made of nylon with nylon fastening, which allow you to visually disguise the lack of 1-2 teeth.
- Acry-free dentures indicated for people who are allergic to acrylic. This is one of the newest dental developments.
Despite the reliability of partial dentures, they should be handled with care. Proper care includes, among other things, restrictions on the intake of too hard foods, chewing gum, and mandatory preventive cleaning after coloring products.
Production of crowns
- these are the elements orthopedic dentistry, allowing you to save a partially destroyed tooth from removal. Thanks to this, the root is preserved, which after some time can be used to install a pin, saving the patient’s money.
Expert opinion. Dentist Yanovsky P.O.: “All types of dental crowns have approximately the same design, hiding the damaged tooth underneath, and repeating its original shape on the outside. The basis for their classification is the material from which they are made. There are about 10 types of crowns, the choice of which depends primarily on their purpose (temporary or permanent) and the patient’s financial capabilities.”
To install any crown, the tooth must be ground down.
The production of stamped crowns is carried out from metal in a very primitive way - using a special press. They are based on durable medical alloys, which include silver, gold, titanium and other materials that are far from cheap. Visually, they are far from perfect, as they have an unnatural color. But at the same time, against the backdrop of more modern technologies they have become cheaper and therefore continue to be in demand for the restoration of 6, 7 and 8 chewing teeth, invisible when talking and laughing.
Plastic products, inexpensive and at the same time natural-looking, are strictly contraindicated as a permanent prosthesis - they wear out quickly, quickly change color, and negatively affect the taste of the food consumed. But with all this, they have one unconditional advantage, which allows the production of a plastic crown to be used for emergency purposes - their production takes only a few hours. Therefore, the indications for the use of plastic are primarily extensive chips and injuries to the front teeth, which require immediate concealment from prying eyes.
– the optimal type of permanent dental prosthetics in terms of price/quality ratio. They are hypoallergenic, reliable, and have a very long service life (up to 15 years). The production of metal-ceramic crowns takes longer and takes several stages - first the dentist cures all carious teeth, then removes plaster casts, prepares teeth, installs temporary structures at the patient’s request. After this, the impression is transferred to a dental laboratory, where an artificial tooth is made, visually almost indistinguishable from the real one. Depending on the number of crowns and the queue for the production of dentures, this can take from 7 to 30 days. In subsequent visits, fitting and fitting of prostheses is carried out.
(E-Max, Cerec), which are popularly called porcelain teeth, are the most advanced, aesthetic and expensive type of dental restoration. The absence of a metal component in these products ensures good light refraction, due to which the crown completely merges with the patient’s dentition. Only a dentist can distinguish it from natural teeth after a detailed examination.
Making a bridge
Dental bridges are structures that make it possible to replace
This is what a metal-ceramic bridge looks like.
several missing teeth. This is not the most The best way prosthetics, since to implement it it is necessary to grind two supporting teeth, which may still be intact and healthy. Crowns are placed on the ground teeth, and the rest of the structure is placed between them, resting on the gum - hence the name “bridge”.
There is a more advanced and expensive method of fastening - with attachments and clasps. Prostheses can be made of metal, metal-ceramics, plastic, and be solid or combined.