Power terminals for large cable cross-sections. Terminals for connecting wires: types and features
Electricians traditionally twist wiring to ensure its reliability and durability. To simplify their work, terminal blocks were introduced. They are created from a pair, or several pairs of contacts, placed in a block, which saves the electrician from twisting. The terminal block connects two pairs of wires with one common contact. The cores are attached inside the connector and fixed, which provides additional reliability of these products. It is important that the terminal matches the intended voltage. An incorrectly selected design may not withstand the stress. Today, terminals are actively used by electricians when installing electrical wiring. Its use does not require much effort, and the pair of contacts is securely fastened. In this article we will understand what types there are terminal blocks for connecting wires.
Types of terminals
The terminal block is actively used in various areas of electrical installation. There are terminals for both individual pairs of wires and for creating system pairs of different levels.
Depending on the installation method, the following types of terminals are distinguished:
Additionally, terminal blocks are distinguished by the number of rows in one connection and by the method of clamping the wires: straight and angular.
According to the type of structure, terminals are divided into:

In the video, a specialist examines several main types of terminal clamps:
Brief overview of varieties
Design features
There are several types of terminals. They are distinguished mainly by the design of the clamp and the method of connecting the conductor, of which there are also several.
Terminal types:
- screw;
- spring;
- block clamping cage;
- end contact of the block;
- knife contact;
- end clamp.
The photo below clearly shows each design option:
In addition, the terminals are distinguished by the type of conductor connection: solid, stranded or flexible. You can study in detail the main types of terminal blocks used in electrical installations, as well as learn how to use them, in this video:
As you can see, the terminal blocks are quite multifunctional. You can choose yourself optimal type blocks for connecting wires. They are increasingly being used in electrical wiring installations.
Manufacturers
The manufacturer plays an important role in the selection of terminals. The selection of materials for the connector, and, consequently, its resistance to stress depends on it. Poor quality pads can melt. The wiring may short out, which will lead to unforeseen consequences.
On average, the terminal block can withstand temperatures up to +105 °C. Terminal block on printed circuit board is more resistant to change temperature regime. Its limit is +250°C. For high voltage applications, heavy-duty, ceramic wiring terminals are used. Their limit is up to +300 °C. Therefore, it is important to choose the right terminal block depending on its purpose.
In addition, you need to correctly select the connector contact to the conductor cross-section. The number of connectors in the terminal block also plays an important role. They should be selected according required quantity. An uncovered connector is potentially dangerous.
Today the manufacturer WAGO Kontakttechnik is very popular. This German manufacturer has proven its quality and affordable prices. WAGO is known all over the world. The brand is used throughout the installation of electrical wiring. Most often, vago terminals are used for connecting lamps. The company is developing the latest methods of attaching to wires. This is a quality of global importance.
Phoenix Contact is big company for the production of electrical equipment. She is also one of the oldest. This company's products are different German quality and accessibility.
Weidmüller is a company that specializes in automatic systems. Among its products there are also terminal blocks. The products of this company are often used in the construction of DIN rails. This narrow profile manufacturer will allow you to create a high-quality wiring connection.
Not bad at domestic market Chinese manufacturers have proven themselves. Chinese manufacturers Degson Electronic and Wanjie Electronic are especially popular. Domestic manufacturers have also proven themselves well in the market. However, products are often domestic manufacturer It costs the consumer much more, and the quality of materials is not always competitive. As a rule, the consumer chooses an inexpensive and high-quality German terminal block. This allows him not to risk wiring.
So we looked at existing types terminal blocks for connecting wires. As you have noticed, today the market for electrical products is flooded with many varieties of terminal blocks, thanks to which you can choose suitable option for your own conditions.
Brief overview of varieties
How to use wiring terminals
Like( 0 ) I do not like( 0 )
Many questions arise when working with electricity, which are related not only to the level of safety, but also to the way the elements are connected. Even experienced craftsmen sometimes have disputes about which method is better to choose in a particular situation. Quite often, terminals are used to connect wires. Let's consider their features and level of reliability.
Variety of terminal types
The wires should be connected very carefully and carefully; if the technology is violated, a short circuit may occur or the devices simply will not turn on after repair. At the connection point, the contacts must comply with the following standards:
- Reliability without additional resistance. That is, it should not exceed the total resistance of the entire wire.
- Mechanical strength that can withstand stretch marks. The coupling point should not be destroyed during any manipulation of the wire.
There are several ways to connect a broken cable, which we will consider in more detail below.
Using the structure
This is the simplest and most common method. You need to take two wires and remove the insulating layer (more than 50 mm), and then twist the exposed wires.
After the cores are securely connected, the open area should be insulated again; for this, PVC tape is usually used. You can also use a “twist cap”.
Note! You cannot connect dissimilar wires in this way.
Related article:
In the article we will consider in detail the design, average cost and material from which the corrugated pipe is made, as well as how to properly work with this device.
Solder connection
The process itself takes a little longer than the structure, but the result is more reliable. In this case, there will be no additional resistance, which still remains when twisting. The soldering also excludes the possibility short circuit, which can occur if the structure is incorrect.
Helpful advice! Tin-lead solder and rosin are used for soldering.
Application of adhesive pads
The glue block is a plate with contacts. This is a kind of connector for connecting wires, and it is used for dissimilar options, for example, copper and aluminum.
Adhesive pads differ in the method of fastening:
- with screw for tightening;
- with pressure plates.
The first option has a drawback - it is the possibility of damage to the cores by the screw, which is especially undesirable when fastening wires with a large number of cores. The second option is more reliable, since the required area is simply pressed with a plate.
Spring terminal block for connecting wires
The fastest fastening method. To do this, you need to remove the insulation layer from the current-carrying core and insert it into the terminal. In this case, fixation occurs using a clamping clamp.
There are many companies that produce these coupling devices. And with their help you can fasten both soft ones with a large number of wires, and with one wire, and of different sections. Using such terminals, you can connect aluminum and copper wires to each other, since plates are used that are coated with a special mixture that prevents the appearance of oxide.
Related article:
In the review, we will consider measurement techniques: current, resistance. How to check capacitors and field-effect transistors, as well as diagnose damage.
Terminals for connecting wires: types and features
Any installer and electrician knows all the main types of glue sticks. In general, they can be divided into screw and screwless. The first option is less reliable, since the screw may damage exposed wires.
All options are placed in a plastic or nylon case (can be kabolite), which provides insulation and contains a contact group (a mechanism for connecting wires).
Note! Often, to use a terminal block, the coupling section must be terminated.
Termination is not required in wires with solid conductors, which are clamped without the use of a ferrule. At the same time, it is necessary to ensure the smallest losses and no heating at the transitions, which is achieved due to several factors:
- using the optimal pair of metals;
- use of quartz vaseline lubricant against oxidation;
- design features terminals involve tightening a wire or lug with a contact group.
Using the right pair involves choosing the metal from which the group of contacts is made. Wires and lugs are made of copper, aluminum or tinned copper. Good contact with these types of materials is provided by steel, brass and some special alloys from which contact groups are made.
How to connect an aluminum wire to a copper wire quickly and easily: photos and videos
Direct twisting of copper and aluminum should not be allowed, since such contact is short-lived and can lead to a short circuit; to solve the problem, use terminals to connect the wires.
There is a way when you can do without a special connector, which requires a screw or nut. This method allows you to connect almost any number of elements, which is limited only by the length of the screw itself. The connection can be made with wires different thicknesses and from different metals, as well as single-core and multi-core options.
Sequencing | Photo example |
---|---|
First, select the screw of the required length. | ![]() |
Remove a layer of insulation from the conductors equal to four diameters of the selected feint. Moreover, oxidized veins must be cleaned to a shine. | ![]() |
Form a ring. | ![]() |
Now sequentially put on the screw a spring washer, a regular washer, a ring, a washer, a second ring, a washer. Finish with the nut, tightening the screw until the spring washer is straightened. | ![]() |
So in a simple way You can connect several wires at once. If you plan to use a stranded version, then first solder it. To make it easier to understand, watch the video at the end of the article.
If you have a terminal block at hand, everything will be much easier. In this case, the resulting connection does not require additional insulation, as is the case with a bolt. To perform this coupling, it is enough to peel off the ends to a length of 0.05 cm from the insulation layer and insert them into the hole, tightening the clamp.
In addition to connecting wires using clamps in terminal blocks, you can use another version of the device that uses the spring principle. There are options for reusable use of the connector, which is very convenient.
Leading Wire Terminal Manufacturers
Even such a device as a terminal should be carefully selected, because the stability of the cable will depend on its reliability and durability. Users have compiled a rating of global manufacturers of such connectors, some of whose models we will consider in more detail.
The TOP 3 leading manufacturers of terminals for connecting wires include:
- Samtec takes the first position (USA).
- In second place is also a manufacturer from the USA – Kycon
- HARTING Germany is in third place in the ranking.
Samtec offers professional tool for crimping terminals for wires - ratchet CAT-HT-281-2430-13 average cost at 30,010. The terminal from Kycon GAX-4-88 will have an average cost of 600 rubles. a piece.
Or you can choose cheaper and simple options, priced from 200 rub. a piece. In any case, select connectors based on the number of cores and elements to be connected.
Video: connecting copper and aluminum wire
Finally
The use of various modifications of terminals greatly simplifies the connection of wires, and different sizes and material of manufacture. You can also use the twisting or soldering method, which will not be as reliable.
When connecting copper and aluminum wires, do not forget that this cannot be done directly; you should use a bolt or connector.
When choosing a connector, look at the number of connectors, the manufacturer and other characteristics of the device. If it is difficult to make a choice on your own, you can seek advice from professionals.
By modern rules PUE 7th edition is allowed to use four methods to connect electrical wires:
Let us consider in detail each of these connection methods.
1. Terminal connections
It is correct to use Wago clamps when branching the neutral and phase conductors. To branch from the protective earthing (PE) conductor, it is necessary to use a different type of clamp, because The main core must not be torn, which is impossible to do with the Wago clamp. For this purpose, it can serve, for example,
knife type clamp. About them a little below.
Screw type terminal blocks
Terminal blocks
Screw-type terminal blocks are available for connecting electrical wires of different diameters. Not used for connecting stranded electrical wires unless they are crimped with brass lugs. The number of conductors clamped simultaneously is no more than 3. The wires for connection are stripped of insulation to a distance sufficient to be clamped under both screws.
During installation copper wires In junction boxes, such terminals are convenient because the connection is compact and can be easily placed in the installation box. However, due to the rigidity copper cores When placing the terminal in the mounting box, a non-contact may appear in the connection. In this case, Wago clamps are preferable.
Screw terminal block for DIN rail.
Read the conditions of use on the terminal block
Another disadvantage of screw terminals is that they must be subject to annual inspection, i.e. tighten once a year, and Vago clamps last at least 30 years without additional maintenance.
When connecting, the cores from different materials, one conductor is passed under each terminal screw, preventing their direct contact. The reliability of such a connection, where only one screw is used to secure each wire, is much less than when using a Wago clamp.
If you need to connect conductors from different materials, then this can be done using a regular nut, screw, washer-grower and an additional washer between the conductors to prevent their direct contact:
One of the types of connections of wires made of dissimilar metals
To switch Zero (N) and Earth (PE) in the electrical panel, busbars with screw terminals are used:
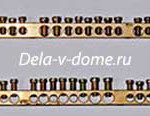
Tires in the shield. On the left is RE, on the right is Zero.
In addition to the shield, an additional PE busbar can be placed at the point of branching into sockets, i.e. in the rooms, kitchen, installing a separate box for it.
Blade type terminal connectors
They are used for inserting branches into the supporting wire. Both wires can have the same diameter, but most often the carrier wire has a larger diameter. Using connectors of this type, branches are made to sockets from an unbroken PE earth conductor. The braiding at the insertion point does not need to be removed from either the supporting core or the branch core. The knife cuts right through the braid. To secure the latch to knife-type clamps, it is sometimes necessary to use pliers to cut through the wire insulation. The connection is reliable and compact.
2. Connections with caps, PPE
If electrical wires from dissimilar materials are connected only using terminals, then wires from the same material can also be connected with insulating caps in addition to terminals, otherwise PPE - with connecting caps insulating clamps.
They come in different diameters, different color and shapes. Made of plastic with a steel spring screwed onto the inner cone. Inside, some types of caps are filled with gel to prevent wire oxidation.
Caps are used for connecting and insulating both multi-core and single-core wires made of the same material, because in them the wires have direct contact, which is not allowed when the wire materials are dissimilar.
To connect, the wires are stripped of insulation to a distance slightly less than the length of the cap, then folded together and twisted with a cap. For reliability, the last turns must be turned with pliers.
The caps indicate the total diameter of the wires being connected. This must be taken into account when choosing a cap, because... otherwise there will be no reliable connection.
3. Welding connections
The most reliable way to connect wires is by welding. Wires should be welded from only one material, either only copper or only aluminum. The welding technology is simple, but the question arises in purchasing welding machine and some work experience.
The wires are stripped of insulation, twisted, and then the end is cut off to equal length for each wire. And only then the end is welded. A small ball of molten metal forms at the end.
It is necessary to insulate the exposed ends of the wires.
The welded connection is compact, reliable in operation and durable. The connection easily fits into the junction box and does not lose contact when placed in it.
4. Branch squeezes
Branch compression "Nut"
Branch clamps, otherwise called “Nuts”, allow you to make branches from the supporting core. Most often used outside the apartment and home due to the large working diameters of the wire.
To connect a branch to the supporting core, this core is stripped to a distance equal to the length metal plates, the branch wire is also stripped. Both wires are placed in the grooves of the plates and tightened with screws.
Compress content
Similar compressions can be used to connect dissimilar wires, i.e. copper and aluminum.
All other compounds that are still used in everyday life and even in some places in production, namely: twisting, twisting followed by soldering, according to modern rules, PUEs are not allowed.
By the way, also interesting:
Copper and aluminum wires. How to connect them correctly to avoid short circuits, oxidation and loss of contact? In this article we will look at the principles of connecting wires and cables, what types of terminal blocks for connection wiresthere are and why it is more convenient and correct to use them than classic screw connections or twists.
Wires are thin metal conductors for electricity. They are produced in coils of 50, 100 and more meters. When creating electrical wiring, you have to break the integrity of the cables, assembling junction boxes, connecting wires to the panel and consumers.
Preparing wires for connection in the box
Note:According to statistics, 90 percent of electrical wiring problems are caused by bad contacts. Electricians have a saying: “the science of electricity is the science of contacts.”
All connections must be carried out extremely responsibly so that there are no bottlenecks. It is not allowed to make ordinary twists or connect copper and aluminum wires directly, since over time the metal oxidizes, the contact surface area decreases, the resistance increases and the temperature rises under load. In some cases, this leads to sparking and fire, short circuits and other unpleasant events, so everything needs to be done efficiently, thoughtfully and thoroughly.
When assembling electrical wiring, the wires need to be fastened according to color, soldering them using screw terminals for wires or connecting terminals. Last option is considered optimal because it saves time, ensures high-quality connection and reliable contacts.
Most connections in the last century were made by twisting - two wires were stripped and twisted together, and then insulated with electrical tape. Such a connection cannot be called high-quality, especially if the wiring was assembled in a hurry and the ends of the wires were not soldered.
Today, twisting is practically not used, but you still need to be able to do it correctly, because it is not always possible to buy terminals for connection. What are terminals (terminal blocks)? These are special connections that allow the ends of wires to be spliced without soldering. If the cable is not connected in a junction box, then the ends are connected at different levels (so that they do not coincide vertically). The connection point is well soldered and first each wire is insulated, and then the entire cable.
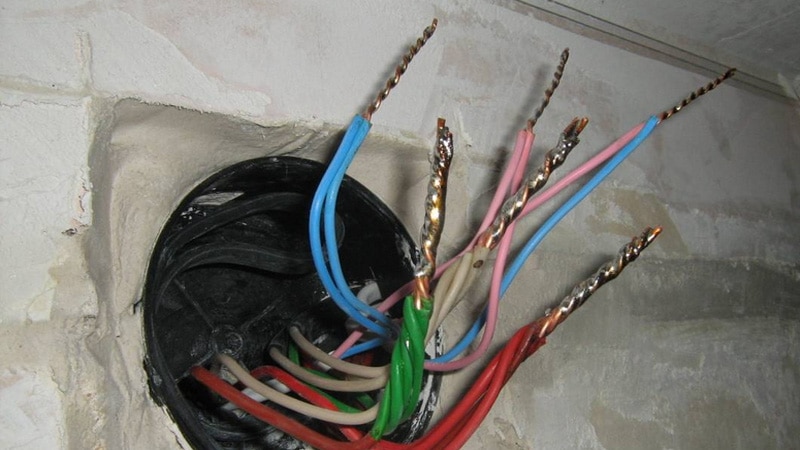
The longer the twist, the greater the area of contact between the elements (soldering increases the area by 5-10 times). It is recommended to twist the wires with pliers to compress them as tightly as possible and improve contact. Metal insulation must be carried out with a reserve, applying electrical tape in several layers.
As you can see, there is nothing particularly complicated about this. But over time, the adhesive on the electrical tape dries out, it begins to unwind and a short circuit may occur. Therefore it is much wiser to usewhich are assembled from plastic that is resistant to temperature changes, ultraviolet radiation and does not corrode.
Such clamps serve for 50-70 years without losing their qualities, their cost is quite affordable, and the connection process is simple and does not require special tools. To connect the wires in the junction box, you can use special caps. They look like little glasses. Installing the caps is very simple - two wires are stripped 10-15 mm, twisted together, and a cap is put on top of them. It covers exposed contacts and seals the ends, improving contact.
When purchasing caps, consider the features of your cable. There are caps for solid and stranded wires, for thin and thick, with a special protective paste inside that prevents oxidation of the metal surface. Remember that copper and aluminum wires cannot be connected to each other, as they quickly oxidize.
Types of Terminal Blocks
There are several types connecting terminals for wires, Therefore, you need to understand which ones will be useful to you. First, find out which cables you need to splice: solid or stranded, cable diameter, single, double or triple. And only after that go to the store.
The classic terminal consists of a plastic housing with a brass insert in the form of a threaded tube that keeps the cable from jumping out.The advantages of the terminals include:
- Ease of operation. In some devices it is enough to simply insert metal stripped of insulation, after which the lock is activated and the wire does not come out.
- Ability to connect wires of different sections. For example, you can connect a 2.5 mm2 cable to a 1.5 mm2 cable.
- Ability to connect wires of different metals, since there is no direct contact between the wires.
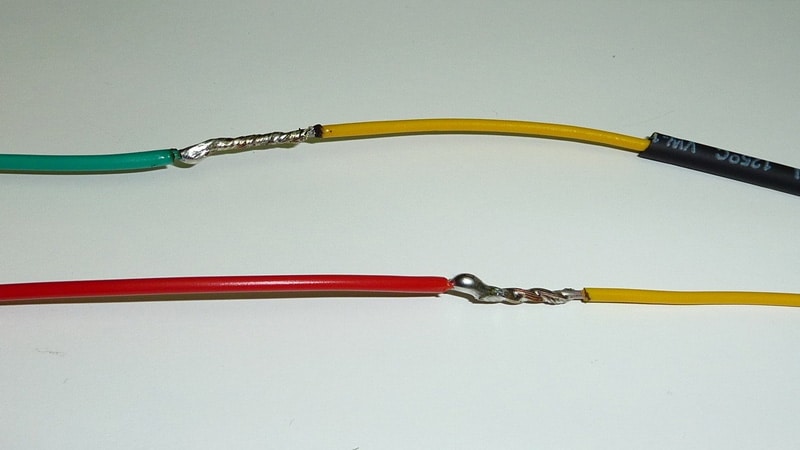
Note:terminals withstand different current, so if you are dragging a line to a powerful consumer (electric boiler, boiler, heated floor), then use powerful terminals.
Terminals have proven themselves in their work - they protect the connection even better than when soldering and using electrical tape. Plastic case does not dry out or break; the clamp ensures a high-quality connection of two contacts and their integrity. The time to install a terminal is only a few seconds, while twisting, soldering and insulating one point can take up to 5 minutes.Cables are connected to terminals in three ways:
- Knife.
- Spring.
- Screw.
Before purchasing, check which terminals are offered to you.The good thing about a knife connection is that you don’t have to strip the wires—the terminal itself cuts through the insulation and reaches the metal. True, installing it requires some effort and experience. Such terminals are often called plug-in terminals; they are used both in everyday life and in the automotive industry.
Spring devices are used both to create wiring in a private house or apartment, and in industry. Using spring connections is the most convenient - to do this, you need to strip the cable to a certain length and insert the metal into the connector. The spring will securely fix the core and prevent it from breaking out even under heavy load. To disassemble such a unit, you need to carefully pry the lever in the terminal with an awl or thin needle, and then pull out the core. But reuse spring terminals for connecting wires not recommended, since they no longer provide high-quality pressing and fixation. Buy a new device - it's very inexpensive.
When buying such connectors, think about how many wires you will need to connect, because they are available in two, three, four and six contacts. When connecting, be sure to not confuse the color of the wires and phase/zero, so that a short circuit does not occur. When connecting switches, always open the phase and connect zero directly to the lamp.
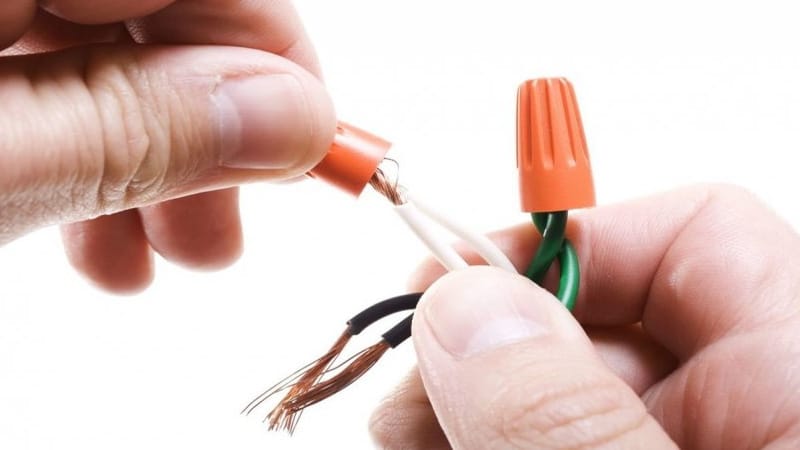
Screw connection terminal block is also popular, although it takes longer to connect than using a spring one. The connection occurs according to the following scheme:
- The ends of the cores are stripped to 10 mm.
- The stranded wire is twisted to make its texture more solid.
- The core is inserted into the connector and secured with a screw from above.
- The operation is repeated on the second side.
Note:The screws are tightened with noticeable force, but do not overdo it so as not to cut the thin copper strands. The wire should not fall out or move in the terminal block.
The disadvantages of this solution include:
- Need for use additional tool(Phillips or flathead screwdriver).
- Difficult to work in confined spaces (if the ends are very short and do not protrude from the junction box, then installing the terminal and tightening the screws will not be easy).
- Installation takes a few minutes. If you simply insert the end into the spring connection, then you need to tighten the screws and waste time.
- After some time, the fastening may become loose due to the stranded wire becoming wrinkled. After a year, it is recommended to tighten the screws to ensure a better connection.
Fasteners for distribution cabinets and boxes
If you need to connect the ends of wires in distribution boxes or cabinets, then you need to use special terminal blocks. Terminal block is device, which consists of a polycarbonate body (not afraid high temperatures and has self-extinguishing properties) in which a copper connector is installed. The housing has holes into which cables are inserted. Terminal blocks can be used to connect wires of different sections and materials, assemble grounding with their help, etc.
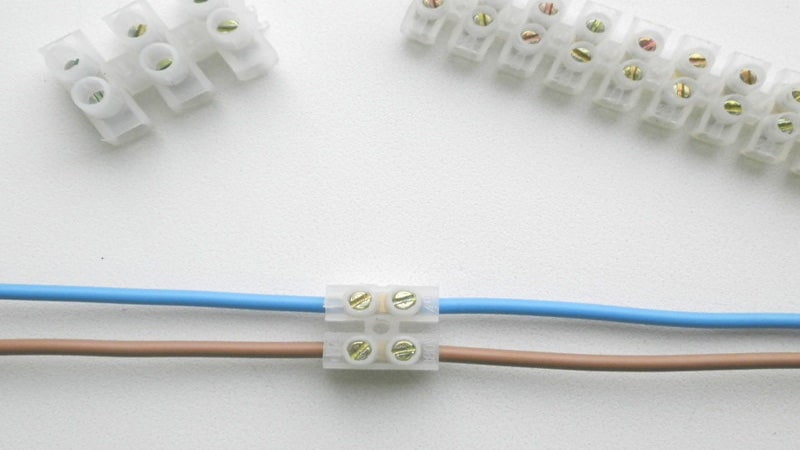
Please note that on the body electrical connection block the current strength that it can withstand is indicated, so be sure to think about what exactly you will have connected or choose strips with boundary values(For copper cable at 2.5mm2 - 25 amperes). Some pads have a special paste inside that protects the bare ends from oxidation and heat.
Fasteners with fuses
To protect electrical wiring and consumers from short circuits and overloads, fused terminals can be used. They have a special holder into which fuses are inserted. If the load increases to critical, it burns out and de-energizes the line, protecting it from overload and melting. Replacing the fuse does not cause any special problems - they can be bought at any electrical goods store.
Terminal blocks for lighting
In principle, these are ordinary terminals, but designed for a small diameter of wires, because lighting is often wired with a 1.5 mm2 cable. The plastic housing of the terminal block can withstand temperatures up to 110 degrees, and the copper tube fastener allows you to quickly connect wires without wasting time on soldering or tightening screws. Since the lighting network rarely has a current strength higher than 16 amperes, the terminal blocks are made small sizes, for 2-4 connections. If necessary, they can be combined with each other if more wires are required. Copper contacts often contain paste to protect the ends from oxidation and remove excess heat.
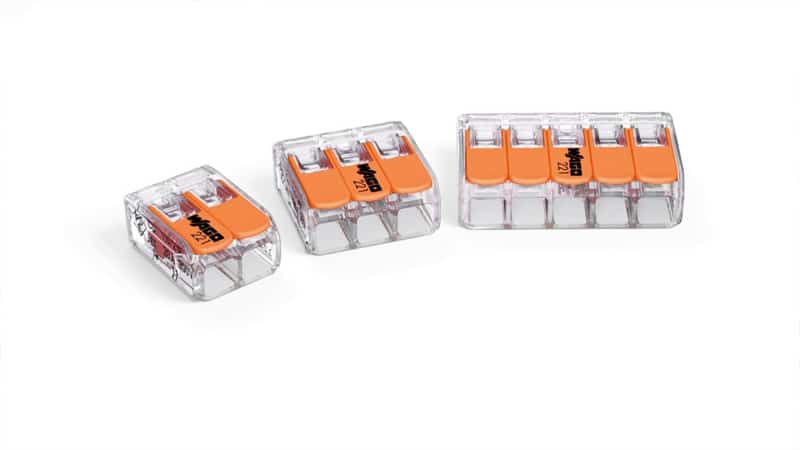
Devices for connecting chandeliers and lamps
When connecting lamps, fans, chandeliers, floor lamps or zone lighting, we also recommend using connecting blocks for wires. This helps speed up the connection process and make it easier. For chandeliers, wide blocks with 4-6 connections are used, for spotlights- for 2 contacts. Since there is no large current in these nodes, the terminal blocks are made small. They are able to effectively remove heat through thermal paste and protect the ends of the wires from oxidation. The connection principle is the same as in the methods described above - screws, springs or knives.
How to properly connect copper and aluminum
Copper and aluminum cannot be spliced together directly because they oxidize very quickly. Good for thisIt turns out that the copper end is attached to the brass tube, and the brass to the aluminum. In this case, the contacts do not oxidize; when heated, the wires do not disconnect or diverge.
It is also practiced to splice two materials together using washers and screws. A washer is placed on the screw, copper wire they wrap it around the screw, put another washer on top, then wrap it around the aluminum, again the washer and the whole structure is compressed with a nut. It turns out that the copper and aluminum do not come into contact with each other, but at the same time they have reliable contact through the washer and screw. More complex schemes with two nuts are also allowed (copper is clamped separately, aluminum separately), but the main thing is that the two materials do not come into contact together, since the contact between them will quickly begin to “float” and disappear. Best to use clamp terminal — it helps to quickly and reliably splice two wires from any materials.
Electrical, construction, screw, self-clamping and spring terminal blocks and terminals for connecting wires and power cables.
Construction and installation terminals – great way carrying out electrical installations. They save time when installing electrical wiring, installing stationary or built-in electrical equipment, are easy to use, and also have a number of useful electrical characteristics that professionals in their field will definitely appreciate.
Degson offers wide choose terminals various designs and properties. The excellent characteristics of the products guarantee a reliable connection of wires, which allows you to always be confident in the electrical installation performed.
Construction and installation terminals
Electrical terminal blocks
Terminal blocks can be of different sizes, depending on the size of the wire being connected. Construction terminals are used for connecting wires with a cross-sectional area from 0.75 to 35 mm 2 and various current loads, up to 30A with a housing made of PA66 and up to 100A with a polycarbonate housing PC with a flammability rating of UL94V-2.
- Modifications with protection stranded wire contact pad;
- Installation of single-core or multi-core wires from 0.75 to 35mm 2;
- Housing PA66: up to 300V, 30A;
- PC housing UL94V-2: up to 600V, 100A.
Structurally, the terminal blocks for the cable are made in the form of a housing made of non-flammable material, in which metal or brass (depending on the model) contact sleeves with screw terminals. There are two types: standard, with open screw terminals for hard single-core wires, and terminal blocks with flags to protect soft stranded wires and provide reliable, tight clamping.
The main advantage of terminal blocks, in comparison with twisting or soldering, is undoubtedly the speed and reliability of installation; the use of terminals can significantly reduce the total time, as installation work, as well as work on further network maintenance. The second advantage is the ability to connect single-core and multi-core conductors of different cross-sections.
Fused terminals
Construction and installation terminal blocks with fuse holder.
The fuse terminal is equipped with a built-in holder for a standard glass or ceramic fuse, size 5x20mm. This type of connection is recommended for use when installing power and low-current circuits for additional protection electrical wiring, or for powering household or industrial electrical appliances not equipped with built-in fuses.
- Stackable connectable structure;
- Separate screw terminal for grounding;
- Standard fuses 5x20mm;
- 400V, 15A.
Connection terminals
Electrical connection terminal blocks for lighting installation.
Wire terminal blocks are widely used when installing lighting, electrical appliances and other equipment and can significantly reduce the overall installation time.
The housing made of non-flammable polyamide PA66, UL94V-0 provides an operating temperature range from -40 to +105°C, copper contact pads provide excellent conductivity, and steel springs provide reliable clamping contact.
It is possible to complete the terminal blocks special paste for connecting aluminum and copper wires. The paste relieves excess overheating of the conductor at the point of contact and protects against possible oxidation.
- Safe connection of copper and aluminum wires;
- Execution options: spring, spring-self-clamping;
- Installation of single-core or multi-core wires from 0.2 to 2.5mm 2;
- 450V, 24A.
- Similar to Wago 224
There are two types of terminals for connecting wires equipped with two types of spring contacts, both have self-tightening properties and are excellent for connecting aluminum wires.
The first, DG224, has only push-cage terminals on both sides, and is used to connect soft stranded wires to each other.
The second, DG222, in addition to the push contact, is equipped with a self-clamping terminal for quick and reliable connection of a rigid single-core wire.
Self-clamping construction and installation terminal blocks for electrical wiring.
Popular terminal clamps are designed for quick and convenient connection and branching of wires when installed in distribution boxes. They perfectly connect single-core wires of any materials and with a diameter from 0.5 to 2.5 mm 2.
To make sure that this terminal has the necessary characteristics, just look at the body mounting terminal. For greater ease of use, the following are written directly on it: the required stripping length, suitable wire diameter and permissible loads by current and voltage.
Terminals for distribution boxes are made in a polycarbonate housing, with iron contact pads and steel self-clamping clamping springs, which ensure reliable connection of wires without additional tools and in just one movement.
- Single-core rigid wires from 0.5 to 2.5mm 2;
- From 2 to 8 wires in one terminal block;
- Simple and convenient installation without special tools;
- The stripping length is marked on the housing;
- Safe connection of copper-aluminum wires;
- Ability to disconnect wires by twisting;
- Convenient hole in the body for the probe of the control tool;
- 450V, 24A.
- Similar to Wago 273
The terminal clamps are great solution for connecting wires, both copper and aluminum, including among themselves, for this purpose it is possible to supply terminal blocks with special paste, which is an undeniable advantage of this type of connection over twisting or soldering.
Terminals for luminaires
Power supply connecting terminal blocks for stationary devices.
In the production of various stationary equipment, such as lighting or ventilation, for ease of installation at the installation site, special power terminals are ideal. This ensures not only convenience, but also savings in materials, effort and time required for the production of equipment and subsequent installation.
On the device side, they are equipped with self-clamping contacts, which simplifies the installation process in production, and push contacts for quick connection at the installation site.
For greater convenience, each terminal is clearly marked; production is carried out with a different number of contacts for connecting from 2 to 5 wires at the same time, which allows them to be used as terminals for lamps, chandeliers, sconces, fans, hoods and other devices.
- Stationary self-clamping entrance (from the side lighting fixture) 0.75, 1.5 or 2.5mm 2 ;
- Mounting spring input (ceiling, wall) from 0.5 to 2.5mm 2 ;
- From 2 to 5 wires in one terminal block;
- Clear, bright markings;
- Can be equipped with an external grounding contact;
- Convenient latches for quick installation on the device body;
- A special hole in the body for the probe of the instrument;
- 450V, 24A.
- Similar to Wago 294 series
All terminal blocks have convenient built-in mounting latches that allow you to quick installation on the device body, and can also be equipped with an additional remote grounding contact with a hole for a screw.
Barrier terminal blocks
Stacked barrier power terminal blocks.
Barrier terminal blocks are an excellent solution when switching power and high-current circuits is required. Suitable for connecting cables of various sizes, from 0.5 to 100 square millimeters.
Used both permanently and in distribution boards, the power terminals are made of black polycarbonate with copper contact pads and steel screw terminals.
- Large selection of types and sizes;
- On a panel, on a block, on a DIN rail, on a printed circuit board;
- Typesetting type;
- Reliable screw clamps;
- Contact covers;
- Contact marking;
- Cable up to 100mm 2;
- Power models up to 800V, up to 200A.
The widest range of barrier terminal blocks from Degson covers completely Various types and sizes, they can be panel-mounted, surface-mounted, DIN-rail mounted, or even printed circuit board mounted, allowing them to be used in a wide variety of applications.
Panel terminal blocks
Stacked spring terminal blocks for the device block.
Spring terminal blocks can be used for surface, panel or wall mounting. junction box. A reliable vibration-resistant self-tightening mechanism inside the panel terminal blocks is suitable for connecting both single-core and stranded wires of any hardness.
Installation of such terminal blocks is carried out using mounting flanges or DIN rails. These terminal blocks for the block are distinguished by their miniature sizes, a convenient dial-up system for connecting single-contact blocks and a wide variety of colors.
They are also distinguished by great wear resistance and a wide range of operating temperatures from -40 to +105 degrees. All this gives them the widest possible use, even in the harsh Russian climate.
- Miniature sizes;
- Reliable vibration-resistant self-tightening mechanism;
- Quick and easy installation of wires by pulling back the spring with a screwdriver;
- Wide variety of colors;
- Also suitable for distribution boards and automatic control cabinets;
- Operating temperature from -40 to +105°C;
- 800V, 24A.
- Similar to Wago 264 series