Ishikawa cause-and-effect diagram. Ishikawa Diagram Method
Graphical method, which is called the Ishikawa diagram, helps to analyze and form meaningful cause-and-effect relationships. Such a system analysis tool for appearance somewhat reminiscent of a fish bone. The diagram certainly contains a central horizontal axis and “ribs” extending from it.
As a supplier, the same employee must ensure that he meets the requirements of the downstream client and provides him with information about his capabilities. In this way, each employee can improve his performance, having a beneficial impact on the entire company.
First - the principle of quality ranking
All activities and processes in the firm must be carried out in such a way as to ensure quality improvement by constantly involving all employees and management in achieving this goal. Regular definition of quality goals down to the level of each employee of the company. It is recommended to set goals with the participation of employees and ensure their commitment in accordance with the level of achievement of the proposed goals.
The Japanese professor Ishikawa came up with his diagram in the middle of the last century, when he was intensely looking for ways to identify the causes of problems that arose in scientific and applied research. The scientist wanted to develop a usable method of systems analysis that would be a visual representation of the problems present in the system.
Determining the strategies and tactics that must be implemented to achieve goals. Involving all employees in the process of continuous improvement of all activities helps promote teamwork. Therefore, when organizing activities, a “process orientation” is recommended, which involves dismantling barriers between departments and creating inter-parliamentary teams to analyze and solve problems.
Company employees should be aware of the need to constantly improve their own business in close connection with end results companies. Communication with customers plays an important role in optimizing solutions, starting from the product development stage and monitoring its behavior during the service process. Personnel training within the company.
The technique proposed by Ishikawa makes it possible to divide the causes of a particular phenomenon into several groups. For example, consideration includes sequentially machines and mechanisms, production methods, materials, external environment. Any of these groups may contain causes of unwanted effects. Each of these reasons can, if desired, be decomposed into smaller system elements, deepening the analysis.
Collaborative management should be encouraged and an open climate should be provided to highlight employees' personalities and stimulate creativity. Keep all processes under control so that product quality is constantly improved. This implies the presence of technical, organizational and personnel facilities that allow continuous monitoring of the process and evaluation of quality results against predefined goals. Also required Information system, allowing the use of information about product requirements, quality characteristics and behavior during use, its impact on environment.
Areas of application of the Ishikawa diagram
Almost immediately after its publication, Ishikawa’s technique found wide application in production management, where it began to be used to analyze product quality and solve complex production problems. Today, the Ishikawa diagram is widely used all over the world, including in the theory of invention, where it is used to identify the causes of technical contradictions.
Quality assurance through systematic preventive measures is the factor that makes the principle of “zero defects” conditional. Taking into account many opinions, the following main recommendations can be highlighted in defining overall quality.
Some of the most well-known experts and the key areas that each covers include the following. We consider the importance of presenting some of the approaches of these so-called quality gurus. Tom Peters reviewed successful American companies to determine the secrets of their success.
The main scope of application of the Ishikawa method is system analysis in order to identify the immediate causes of an existing problem. The diagram can be successfully used for element-by-element analysis of production and marketing processes at an enterprise, their systematization and structuring. IN Lately The technique is increasingly used in brainstorming.
He determined next questions which are published in his books. Among the most notable expressions are: “Quality is what is fit for use,” and quality costs are “gold in hand.” Quality is not accidental, but must be planned; Most quality problems are due to poor management rather than poor production in the factory. Key elements of implementation strategic planning quality in the enterprise are.
Edwards Deming's Principles
Identification of clients and their needs; setting goals; planning processes capable of achieving quality objectives; implementation of quality improvement measures. Quality planning should include the following steps. Defining specific goals to be achieved; establishing programs to achieve goals; assigning clear responsibilities for each goal; receiving rewards for results obtained. Deming gives great importance responsibility of management, both at the individual and enterprise level, for maintaining quality.
How to build an Ishikawa diagram
First, the researcher clarifies the problem, its essence and complexity. After this, the starting point of the analysis is constructed, which looks like a horizontal arrow pointing to the right. At the tip of the arrow is a clearly defined and clearly stated problem.
Additional arrows are drawn to the center line at a certain angle, each of which indicates one of the possible causes that caused the problem. If during the analysis it turns out that the causes are in turn due to deeper factors, each of the arrows can branch out.
Principles of Kaoru Ishikawa
He introduces the concept of "deep knowledge", a term used to describe accumulated insight and insight. Consistency of purpose; Responsibility for changes; Incorporate quality into the project and reduce the need for inspection; Continuous and definitive improvement to reduce long-term costs; On-the-job training Leadership training; Removing fear; Removing technical and commercial barriers; The right to professional pride; Training every employee to achieve change. Cause-and-effect diagrams—allow for a graphical representation of a problem and possible causes.
By constructing a detailed graphical display of cause-and-effect relationships, you can clearly imagine the entire system in the dynamics of causes and effects that influence, for example, the result of production activities or the management of an enterprise. Very often, such a visualization tool helps to identify significant factors that escape attention with another method of analysis.
The chart was developed as a powerful diagnostic tool in the field of quality thanks to Japanese expert Kaoru Yushikawa. He used the diagram to help executives solve a number of problems during brainstorming sessions. Classifies information obtained by any method; Allows you to analyze ideas by simply removing one branch in a line; Emphasizes the need for information for analysis; It can avoid collecting unnecessary data. Men; Materials -; Methods -; Environment. . The diagram causes an effect.
What can be achieved using the method? Creating ideas; Visual method records; Identification of unrelated relationships; Identifying the origin of the problem. Phases of diagram construction. A team has been created; The nominee is appointed to be responsible for marking team members; Possible causes are listed in the diagram and the most likely one is analyzed first; The diagram should not be overloaded; Let the diagram be hidden from view; It can be completed in other meetings; Analyze the diagram and other meetings if ideas still exist. Initially, the idea is not deleted. . Solving problems requires a structured and planned approach.
Axial time- a term that underlies the entire cultural worldview of the German philosopher Karl Jaspers. He designated the axial time as that period in the history of mankind when the mythological views of people gave way to rational, philosophical thinking, which became the further basis for the development of modern man.
Quality training
Diagram of problems. An organization's human resources are often cited as the most important asset that does not appear on the balance sheet. However, the quality and method of human resource management have important for the success of the organization.
Determining Training Needs
Training has been defined as a strategy for promoting behavioral change by creating an opportunity to learn.Most training is carried out continuously, without taking into account its needs or without taking into account current shortcomings or future needs. The only way to follow is to analyze the current needs and their level. Training needs can exist at at least three levels.
Jaspers' research suggests that all the teachings that arose during the Axial Age are distinguished by a high degree of rationalism and man's desire to rethink all the foundations of his previous existence, change customs and traditions. Those civilizations that were unable to rethink their worldview in the light of the Axial Age simply ceased to exist (for example, the Assyro-Babylonian civilization). Jaspers believes that the Axial Age time- This is the period between 800 and 200 BC. Recent research data also confirms that the period 800-200. BC. was of particular importance in the development of the world system. During this period, there was a sharp leap in the development of global urbanization, and the level of literacy of the population increased. During the Axial Age world system transformed into a qualitatively new state for itself. In the key centers of world culture during this period of time, religious and ethical teachings, completely different from everything that was before, developed, the basis of which were fundamentally different values. These values were deep and universal, which allowed these teachings, although in a slightly modified form, to survive to this day (Confucianism, Buddhism, Taoism). Axial time a turning point in a person's perception of himself, it is time when a person first begins to perceive his essence and analyze his own thinking. An attempt at self-knowledge underlies all the fundamental changes of that time. It was in the course of attempts to realize one’s existence, to define key moral concepts: good and evil, the meaning of life and death, that a new cultural era was born. Thus, the concept of axial time implies a certain segment in the development of world culture, during which development trends and cultural values of humanity, which leads to the beginning of a new era in the development of the world system. Thus, Jaspers believes that modern cultures are facing a new round of axial time, the result of which will be a single culture on a planetary scale.
Organization level; Professional level; Individual level. . Training needs may exist for two main reasons. Typically, training needs analysis proceeds from the general to the specific. The worksheet states the purpose of each message and highlights its main functions. A job specification breaks down tasks into tasks and activities, defining the attitudes, abilities, and knowledge required to complete the tasks. Depending on the position, performance may be assessed different ways, and often a combination of several methods is the most comprehensive way.
Sources:
- www.terme.ru
Modern technologies production management and quality management allow you to analyze production processes extremely effectively. One such method: the Ishikawa diagram, is successfully used in many enterprises around the world.
The learning cycle - a systematic approach
Questionnaires; Structured interviews; Observations, measurements; Expression of gratitude. Numerical Data Trends; Business plan; Workforce planning. . In most situations where a certain outcome is expected, success is more likely to be achieved if the project is approached systematically. The learning cycle is a method used for targeted learning and it is important that all participants understand the next steps. Although not all lecturers will be concerned with developing and preparing complete sets educational materials, the miniature process must be followed for each session presented to the group.
A state diagram resembles a block diagram and represents the process of changing an object as a result of transitions. This concept was introduced several decades ago and has been constantly improved with the development of computing technology.
Analysis.
- What is the overall learning goal?
- What are the elements won by participants at the end of the training?
- Were appropriate questions asked at each stage of the cycle?
- Were the answers correct and complete?
- Did he really study?
- Was the training as effective as possible?
- Are participants able to use new skills?
Basic Concepts
A state diagram is an abstract representation of a process. It is often used in computer science to model the flow of programming languages. It can also help analysts create a business process map. Elements of a system diagram are usually called objects that can undergo changes in state. The most popular language for writing state diagrams is Unified Modeling Language or UML. This language allows you to track the process throughout the entire build. It is usually used to describe the behavior of the system as a whole. A state diagram helps keep track of objects using various symbols. It usually does not describe the interaction of objects.
This phase may be lengthy, but as with other aspects of training, ultimate success will be proportional to the effort invested in preparatory stage. Workforce development can be viewed in a broad context, focused on achieving personal development in all aspects of life, taking into account existing potential, recognizing that life in the workplace cannot be considered isolated.
An organization that neglects workforce development will be punished by losing the potential of employees who will perform at a lower level of performance than they would have been capable of or even lost best employees, sent to organizations where they are encouraged and grow sustainably.
Features of creating a state diagram
UML diagrams usually show how an object behaves in various options developments and several symbols are often used for identification various elements. A state diagram is very similar to a flowchart. Typically, it has a large dot at the top that represents the initial state of the object. Changes in state can be shown as circles, with the name of the object, variables and actions separated from each other. Horizontal lines are generally used to separate each one.
What should the organization do? What should management do? Managers must determine their training needs, taking into account the need to provide expert advice and assistance. As part of their daily responsibilities, managers must prepare and guide their subordinates.
What should an employee do? Each individual is responsible for his or her own personal development and the organization should encourage any personal initiative to expand experience and develop new skills, both within the organization and through external training programs.
Straight lines in a state diagram can connect elements. Lines usually define transitions. Very often these lines have arrows at one end to show paths from one state to another. At the bottom of the diagram is a large black dot in a circle. The whole diagram can describe complex chain events and the conditions under which they occur. There may be more than one such condition.
Needs assessment and analysis are questions that need to be answered. Managers and organization.
- He is pleased with his post and its prospects.
- How can he improve his performance?
- How can this help?
- What do they want to do?
- Is the head happy with how he is progressing?
In self-improvement: - time planning; risk taking; idea creation; When working with others: - obedience; security feedback; encouragement; disciplinary dialogue to solve problems while performing activities. Improved qualifications and technical knowledge.
The process depicted in a state diagram is usually defined by the changes that occur. Some object states may be unlikely. Sometimes multiple transitions lead to the initial state, which can lead to confusion. In this case, one diagram can be enclosed within another. This is then called a superstate. This format makes the state diagram easy to read if the events and transitions in the system are complex.
Conclusion
A state diagram can represent the results of machine operations or the operation of many mechanisms in production system. It can also help the teacher think through his learning programs based on the material that is in stock. Semantics
or rules are often applied to state diagrams. There are alternative rules and even variant models that can be used depending on the problem. For example, manufacturing process For electronic device, like a stopwatch or controller.
Video on the topic
In the process of work or training, one often encounters certain graphic diagrams, for example, with diagrams. This is a commonly used diagram used to display shares, percentage anything. And knowledge about constructing such diagrams will be quite useful.
Instructions
To create a diagram, use the program Microsoft Excel. Of course, Microsoft Excel has a feature for creating automatic charts. But this is unlikely to suit a person who wants his scheme to be unique and exactly the way he intended it. With a little effort, you can create your own chart in Excel using all the same features.
Create a new chart and get rid of everything you don't need. It should be easy to understand. You should only use two colors. For example, do gray background and dark blue columns displaying indicators. These two colors are the most pleasing to the eye and do not create a contrast with each other. The information will be legible and understandable. You will also need to note the increasing growth of parameters.
An Ishikawa diagram is a popular way to graphically represent cause-and-effect analysis. Outwardly, it resembles a fish bone or skeleton. Therefore, the instrument is often called a “fishbone”.
The author is Japanese chemist Kaora Ishikawa. The method was developed back in the early fifties. At first, analytical techniques were used only within the framework of quality management. Subsequently, it began to be used in other problem areas.
Ishikawa diagram in an enterprise
The main goal of the method is a group search for problems and their causes. The Ishikawa diagram (“Ishikawa” is another transcription) is included in the Japanese Industrial Standard (JIS) as a cause and effect graph showing the relationship between a quality indicator and the factors affecting it.
The technique is intended for the initial ranking of factors affecting the problem under study. This is the result of analytical work. For example, manufacturing defects have increased. This is a problem, an object under study. The manager gathers those responsible and asks them to allocate possible reasons this problem. Then the factors that led to the occurrence of a particular cause are analyzed.
Ultimate goals analytical method Ishikawa:
- identification of all factors that influenced the occurrence of the problem;
- visualization of connections between the problem and possible causes;
- placing emphasis for analyzing and solving the problem.
Ishikawa Cause-Effect Diagram (Fishbone): Example
A classic chart template looks like this:
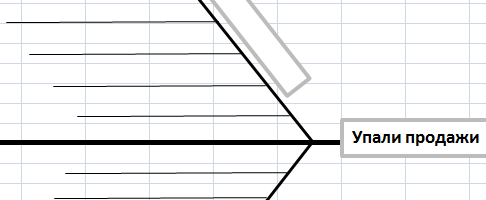
It is important to identify all factors during analysis. Even those that seem insignificant. Subsequently, the factors are assessed and ranked. The task is to identify the most significant ones, which had the greatest impact on the decline in sales.
To rank factors, you can use, for example, the Pareto method.
How to build an Ishikawa diagram in Excel
It is quite difficult to construct an Ishikawa diagram using Excel. But you can analyze the weight of each factor. And based on the schedule, find the optimal way to solve the problem.
Let's look at our example. The found factors do not have a numerical expression. For illustration, let's evaluate them in points.
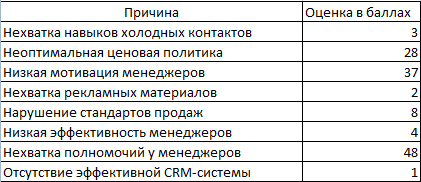
Let's sort the numbers in ascending order. Let's calculate the share of each factor with a cumulative total.
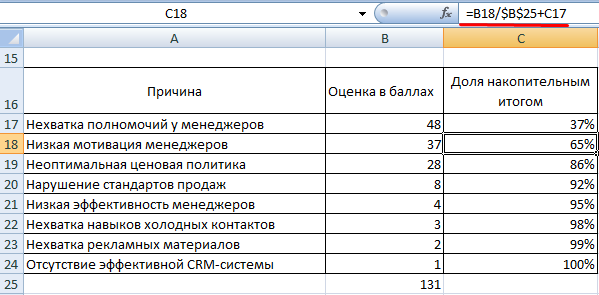
Let's illustrate the scores in the form of a histogram. And the share is in the form of a graph with markers.
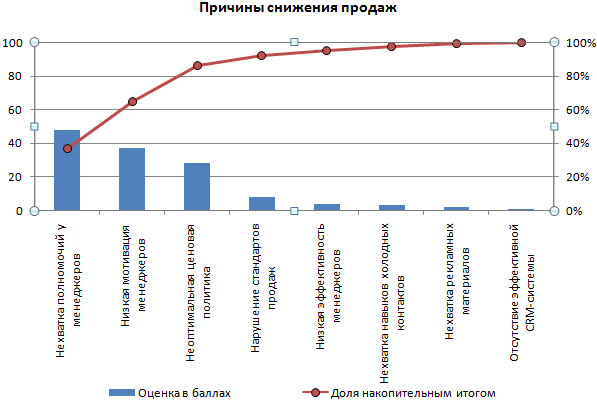
The diagram shows that in order to solve the problem that has arisen, you need to work mainly with the first three factors.